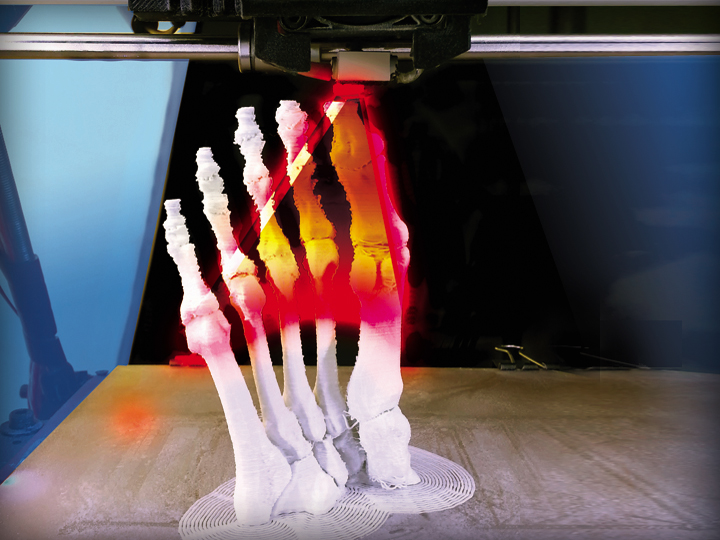
Promise of 3-D printing looms – in duplicate
Published on Monday, November 9, 2015
Published in News Stories on November 12, 2015
It's a printer without paper, without toner or cartridge or ink; when the print job is finished, you can't read it, because there's no print to read.
But you can wear it, make music with it, drink from it, eat with it, chew with it or swallow it with a glass of water, or even replace a missing limb with it. And there's much more to come.
It's called 3-D printing, but “three-dimensional” doesn't begin to cover the depth and breadth of its reality and revolutionary promise, especially in the fields of health care and medical research: living tissue, perfectly fitting prosthetics, tailor-made medications and simulated organs.
“The potential for drug testing using this technology is huge,” said Dr. Radhika Pochampally, associate professor of biochemistry and director of the UMMC Cancer Institute's Non-embryonic Stem Cell Core. “It can even be used to replace organ systems.”
At least two UMMC schools - dentistry and health related professions (SHRP) - are exploiting 3-D printing, which has been around for at least three decades but is beginning to boom, in part because related patents have run out.
A member of the high-tech family called “additive manufacturing,” this tool creates 3-D, solid devices and replicas expressed in a digital file or a mere drawing. Without any knowledge of the process, a first-time observer might believe it weaves substance from thin air.
The truth is, a 3-D printer coins its handiwork by putting down successive layers of material, like a highly focused, overachieving glue gun: Each tier is a cross-section of the final product.
Sarah Bond, an OT student, worked with Robin Parish, an assistant professor of OT, to produce this 3-D pattern for a prosthetic hand.
Taking advantage of this technology, Sarah Bond, an occupational therapy (OT) student, has come up with models for one-handed bottle openers, a cup holder attached to a crutch, a finger splint and more. Working with Robin Parish, assistant professor of OT, Bond also helped put together 3-D-printed patterns for prosthetic hands.
“The kids love them because they look like robot hands,” said Dr. Lorraine Street, professor of OT.
Bond is sold on 3-D printing because, for one thing, its creations are quickly and accurately duplicated.
“Without the 3-D printer, you would make these devices from household items, but those are not reproducible,” she said. “We (OTs) are constantly trying to help people with adaptive pieces, but the tragedy is that we put in a lot of time for one device.
“With 3-D printing, we have the ability to share our designs, and we're able to help more people.”
For the purposes of SHRP students like Bond, the 3-D printer housed there is mainly a teaching tool. It produces prototypes, not actual articles for everyday use.
“And it's not a biomedical 3-D printer, the kind you see at Cornell or on 'CSI,'” said Terry Pollard, assistant professor in the school's Health Sciences Program and director of instructional development and distance learning.
“Ours is used mostly for instruction, mainly for the OT and dental hygiene programs.”
For instance, students visiting the office of Dr. Beckie Barry, professor of dental hygiene and the program chair, can examine a space-age, 3-D printed product that reflects an old-school need: a set of lower dentures.
And Dr. Hamed Benghuzzi, professor of clinical health sciences in SHRP, is impressed with 3-D-printed versions of drug-delivery devices that are placed under skin or muscle.
“They're used for classes, for teaching the students here, but they save time and costs, compared to producing ceramic versions which can take a week to make,” he said. “On the 3-D printer, it takes only one hour.”
Any of SHRP's academic programs could profit from getting acquainted with the printer, Pollard said.
“It can help you solve problems - 'What can I build? What can I make?' Many times, it just means being creative.”
When Pollard began searching for a 3-D printer a couple of years ago, Michael Kuiper, IT project manager with DIS, recommended the Stratasys Objet 24.
“It's an entry-level business printer which I knew SHRP would be much more satisfied with over a consumer [home-use] one,” Kuiper said. “Each line it prints out is finer than a human hair.”
The primary material, or “ink,” for manufacturing an artifact is a polymer called vero white. Layer by layer, the printer jets squirt it out in liquid form, which hardens under ultraviolet light, said Ron Landreth, a support analyst for SHRP and the man students and faculty see for adventures in 3-D printing.
“It also uses a support material that forms a base. When the item is finished printing, I scrape off the base with a scraper. It's kind of like cookies on a pan.”
But these cookies need washing. For that, Landreth turns to a contraption about the size of a dorm-room refrigerator to also dry and cure the designs that are often inspired by ideas available for free on such websites as thingiverse.com.
The Object 24 is about the size of a regular office printer and today costs up to around $24,000, said Tony Castillo, a Stratasys operations management representative. With more advanced models, he said, “you're looking at digitally mixed materials, different colors and texture. For some machines, there is no limit. It's whatever can be imagined and created.”
That includes printing an entire house in China, or a bridge in Amsterdam; these things have been done.
While the possibilities, so far, are much smaller here at the Medical Center, they're also significant. The School of Dentistry has embraced several different types of “rapid prototyping,” said Dr. Jason Griggs, professor and chair of the Department of Biomedical Materials Science and associate dean for research.
The images of computer-designed dental crown molds, displayed on the monitor of Inge Knight, instructor in the School of Dentistry, are used to produce dental crown molds.
One brand-new development is a partnership with a 3-D printing group at the Center for Advanced Vehicular Systems at Mississippi State University, where robots and other cutting-edge projects lurk.
“Their machine can build any part that has already been computer-designed,” Griggs said.
Within the dental school itself, in the fourth-floor teaching lab, a printer about the size of a toaster oven is popping out molds for crowns that are designed on dental software. Printing, or spraying, with a liquid polymer, this system cuts out the need for the traditional, time-consuming technique that constructs a crown by a build-up of wax.
Dental students are still learning this “lost-wax” method, said Dr. Scott Phillips, associate professor of care planning and restorative sciences.
“We don't have the scale yet to do widespread 3-D printing,” Phillips said. “But waxing can be difficult. It's easy to computer-generate this instead.
“You can photo-shop a crown, basically, and perfectly match a crown with a tooth. It saves time if you're doing multiple crowns.”
While the dental school's printer is drafted mostly for class projects and to spit out smaller crowns, larger models elsewhere can grind out dentures, orthodontics and even reproductions of a patient's skull or jaw to help surgeons better plan an operation, said Inge Knight, a School of Dentistry instructor.
“When it comes to the technological part of dentistry, the hard part is keeping up. A larger printer is kind of on our wish list.”
These 3-D printed models are, clockwise, from top, the skeleton of a rat, the down-sized hemispheres of a human brain and a representation of the molecular structure for methamphetamine.
Some Medical Center staff are working on projects with 3-D printers outside the university. And faculty members and researchers in other departments and programs have bent Kuiper's ear about this innovation as well.
“I would love for us to get more involved in this at UMMC, and I'd love to be a part of that,” he said. “As more areas here embark on this technology, I believe it will spread like wildfire.”
For her cancer research, Pochampally, for one, is ready to turn up the heat.
“I'm especially interested in 3-D applications for bone cancer, replacing bone material that had to be removed,” she said.
At Spain's Salamanca University Hospital, doctors reported recently that they had implanted into a cancer patient a customized rib cage and sternum that are made of titanium built by a 3-D printer.
“In certain cases, where there is very little risk for metastasis (the spread of cancer to other parts of the body), this could potentially offer a cure by opening up possibilities for replacing primary tumor organs,” Pochampally said. “It would at least improve a person's quality of life.
“You cannot get cancer on titanium.”
For now at least, she'd like to have access to a 3-D diagnostic tool for cancer. But a printer that has multiple uses would be ideal, enabling researchers and others across the campus to develop their projects as well.
“I'm working on a proposal for one now,” she said. “3-D printing brings a lot of advantages to the university. It offers a lot of potential. It puts us at the forefront of research.”
To find out more about a multiple-use 3-D printer, email Dr. Radhika Pochampally at rpochampally@umc.edu.
To find out more about 3-D printing, visit the following websites:
• http://news.sciencemag.org/sifter/2015/09/watch-cancer-patient-receives-world-s-first-3d-printed-sternum-and-ribs
• http://drexel.edu/research-enterprise/impact/fight-cancer-3d-printing
• www.cnn.com/2015/10/06/health/3d-printed-heart-simulated-organs/index.html